Ibanez Cavity Depth

Ibanez Cavity Depth Definition
Build an Electric Guitar - Without the Fancy Tools
I think I need only drill down to a depth of 5mm or so, so being super-perpendicular isn't going to be a massive requirement. Also, as this is an Ibanez RG, with it's spring cavity and trem back-rout, there's not a whole lot of wood there to start with, and I'd like to keep as much as possible in order to give the pickups something to resonate. Ive always wanted an Ibanez S470, and finally pickedup a used one for a great price. Yuletide legends: who framed santa claus crack. I like the sound, but have decided I want to put in a set of EMGs (85/S/81). I know how to wire them and everything on the electrical side, but Im having a hard time trying to figure out where to put the battery. Control cavity's plate for ar200, ar300: pc: 4pt1cax2b: control cavity's plate for ax125, ax7221: pc: 4pt1cdt2: control cavity's plate for dt200: pc: 4pt1cer3b: control cavity's plate for edr: pc: 4pt1cic2: control cavity's plate for ic200, ic400: pc: 4pt1cjs3b: control cavity's plate for js100: pc: 4pt1cmmm3: control cavity's plate for mmm1.
The DiMarzio® Air Norton™, True Velvet™ and Tone Zone® pickups offer depth, warmth and rich dynamics when combined with the 5-way pickup switch. The RG1070FM utilizes Belden wiring and copper shielding inside the control cavity for noiseless operation.
Wood Selection
The most common body woods for electric guitars are mahogany, alder, walnut and swamp ash. Swamp ash is my favourite body wood due to its lightweight and great mid-range tone. You will need two pieces of 8/4 stock for the body, at least 21'x 7 ½' finished dimensions.
The neck is most commonly made from hard maple or mahogany. Walnut is also used, giving a more complex acoustic-like tone. Neck wood needs to be straight grained and free of knots. Quarter sawn is best but flat sawn is also used. You can also use flat sawn stock and laminate it to get a quarter sawn neck blank; this is the method I use. A laminated neck is stiffer and more stable than a one-piece neck. You may use different combinations of wood to make different patterns of laminations if you wish. Rough neck stock should be about 36'x 5' x 4/4 and the finished thickness of the neck blank is 21mm.
The fingerboard should be quarter sawn with straight grain, free of knots and heavy figure (an exception to this is bird’s eye maple). I recommend using rosewood, ebony or Ziricote. If you decide to go with a maple fingerboard it will need to be finished with a lacquer or urethane clear coat before the frets are installed. If left unfinished, maple fingerboards will quickly become dirty and stained with frequent playing.
For this project I suggest using a pre-slotted and radiused fingerboard from Stewart MacDonald. The spacing of the frets is too critical to risk. This will save you from having to buy somewhat costly fret scale templates, radiused sanding blocks and a fret slot saw.
Start by Making the Templates
While you’re building this guitar be sure to reference the hardware you plan on using when routing all the cavities. Make a point of obtaining all hardware before you start the project so there are no surprises later.
Unlike most guitars, this one is made using basic woodworking tools. No fret saws, gauged nut files or any other fancy tools here. A router will do most of the work, with a bandsaw, drill and some basic sanding equipment filling in when needed.
Master templates – The first thing to do is make a master neck and body template from ¾' MDF. For this style of guitar the neck is 1 ¾' wide at the nut and 2 5/16' at the heel. The distance from the end of the neck to the nut is 18 ¼'. The total length of the neck is about 24 ½', though the length may vary depending on your headstock design. The body is about 18' long and 13' at the widest point. When it comes to designing a solid body guitar the sky is the limit. Keep it traditional or get as wacky as you like. The shape of the body doesn’t affect the tone of the guitar as greatly as it does with acoustic guitars. These plans are based around a Les Paul-style guitar.
Cut the MDF templates out on the bandsaw and clean up the body and headstock profile on a spindle sander. To get perfectly straight neck edges, screw a piece of MDF (approx. 20' x 6') with a jointed edge to the neck template right along the pencil line of one edge. Use a flush trim template bit in the table router to trim the edge of the neck. Repeat on second edge. Clean up the end of the neck template with a disc sander.
Draw centerlines on both the neck and body templates. Drill index holes in the neck and body templates with a ¼' brad point. These index holes will be used to align and pin the templates to the wood for all machining processes. The body requires two index holes, on center, that need to be inside the neck pocket and inside the bridge pick-up cavity so they will be hidden. The neck template requires two index holes as well; positioned about 2' in from the heel end, and about 2' from the nut (toward the heel). Exact positioning is not critical, however, the holes must be far enough off center to be outside of the truss rod slot.
Master templates – Take care to make these templates carefully because they will be used repeatedly to machine the body and neck of the guitar.
Body Index template – In order to rout the neck pocket and pick-up cavities, the routing templates need index holes outside of the body profile, since there are no other places for concealable index holes on the top of the guitar. This will be the master from which all routing templates are based. Cut a piece of clear acrylic (plexi-glass) to 21'x 4'. Scribe a centerline the length of the piece with the back edge of an exacto knife. Clamp it to the body template to drill index holes. Drill a second set of index holes outside the body profile. These will be the index holes used for all body routing jigs.
Body index template – A number of jigs will reference off this template in order to keep the body free of holes.
Control Cavity/Cover plate recess routing template – Draw a centerline on a 21'x 14' piece of ¾' MDF. Making sure the centerlines are aligned, clamp the acrylic body index to the MDF as a drill guide. With a ¼' brad point, drill the inside and outside sets of index holes through the MDF. With ¼' steel pins, attach the body template to the MDF and trace the body profile. Mark your control layout on both sides of the centerline. On one side draw your control cavity, on the other side draw the cover plate. Drill out the center with a large forstner bit, then spindle sand to shape. Alternately, use a jigsaw to remove the waste before sanding to shape.
Cavities – The cavities are made by running a flush trim bit off of this pattern.
Neck Pocket routing template – Draw a centerline on a 21' x 10' piece of ¾' MDF. Clamp the acrylic body index to the MDF (centerlines aligned) as a drill guide. With a ¼' brad point bit, drill the inside and outside sets of index holes about15mm into the MDF. With ¼' steel pins, attach the body template to the MDF. Trace the body profile. Mark out the neck pocket (exact size of neck template).
Frame out the neck pocket with pieces of MDF that have been trued on one edge. Pre-drill and counter sink the MDF pieces, then screw them to the template. Check the fit with your neck template. With a ½' template bit, rout out the neck pocket. Remove the frame.
Frame it then route it – Create the framework with straight scraps. The router bit will follow this frame to produce the neck pocket.
Pick-up Cavity routing template – Draw a centerline on a 21'x 10' piece of ¾' MDF. Clamp the acrylic body index to the MDF (centerlines aligned) as a drill guide. With a ¼' brad point bit, drill the inside and outside sets of index holes about 15mm into the MDF. With ¼' steel pins, attach the master body template to the MDF. Trace the body profile and remove the template. Next, pin on the neck pocket template. Trace the neck pocket and remove the template. Mark out the pick-up cavities on the MDF pick-up routing template. Frame out the pick-up cavities with pieces of MDF that have been trued on one edge and fasten them to the template. With a ½' template bit, rout out the cavities. This is done in two steps to get the shape required; one pass wider and shorter, the second pass narrower and taller. Framing and routing the cavity as two separate rectangles, with four larger pieces of MDF, will produce a more uniform cavity than using eight smaller pieces and routing the cavity all at once.
Pick-up cavity, step one – Frame the cavity to be routed, then machine the first cavity.
Pick-up cavity, step two – Re-frame the cavity at a slightly different size and route out the material.
Pick-up cavity, complete – The pick-up cavity in the template is complete. Test its dimensions with the hardware to make sure it is the right size.
The Body
Begin by cutting your 8/4 body stock to 21' lengths (or longer depending on your body shape). Joint the best edge and bandsaw to at least 7 ½'. Joint one face. If you do not have a thickness sander, you will need to plane your stock to final thickness before glue-up. Standard thickness is about 41mm. If you choose to put a book-matched top on your guitar, the back should be about 35mm with a 5mm thick top.
The real deal – Use the template to rout the pick-up cavities in the body.
Glue up
Be sure your glue edges are true. Run a heavy bead of good quality wood glue down one edge and spread to cover the entire surface and clamp until dry. Use MDF cauls and C-clamps to keep the body halves flush. During glue up be sure to use wax paper or poly film between the cauls and the body blank! Once the body has dried for 24 hours, scrape the dried glue squeeze out and sand both faces clean and flat. Lay the body index template on the top face of the body and align the centerline with the glue line. Clamp it in position and drill the outside set of index holes with a ¼' brad point bit. Drill the inside set of index holes 10mm deep. Pin the body profile template to the body blank and trace the profile. Rout the pick-up cavities.
Pin the pick-up template to the body. Always use steel pins when routing.
With a ½' template bit, rout the cavities 20mm deep, in two or three passes. If you don’t have a plunge router, drill a starter hole to full routing depth with a forstner bit to allow the bit to plunge to full depth before routing.
Rout the Neck Pocket
Pin the neck pocket template to the body. With a ½' template bit, rout the neck pocket 15mm deep. Take at least two or three passes to slowly remove all the waste. Drill the control holes according to the shaft size of the pots/switches you’re using. They should be 10mm deep.
The neck is next – Continue routing, this time removing the waste to create the neck pocket.
Rout the Control Cavity
Pin the control cavity/cover plate recess template to the body. With a ½' template bit, rout the cover plate recess 4mm deep. Flip the template and push the pins through to the other side. Pin the template to the body and with multiple passes rout the control cavity 35mm deep. You may have to shim up your template to rout the cover plate recess, and remove the template to rout the full depth of the control cavity.
Carefully bandsaw the body profile and spindle sand to final shape.
Clamp the neck template into the neck pocket and measure out the bridge and tailpiece locations. The distance from the nut to the bridge is 24 ⅝' (treble side) and 24 13/16' (bass side). The tailpiece is 26 ¼' from the nut. Measurements are to the center of the post hole. The manufacturer of the hardware should specify post hole spacing. Drill the bridge and tailpiece holes.
Ease the edge of the body with a ¼' round over bit. Use your jack plate to mark and drill the jack mounting holes with a ¾' forstner bit. Drill the pilot holes for the strap pins. The pick-ups can be mounted with rings or straight to the bottom of the cavity without a ring. Mark and drill the pick-up mounting holes. I mount the pick-ups without rings.
Drill a hole for pick-up leads and ground wire. With a long ¼' bit, drill from the pick-up cavities to the control cavity. With a long ⅛' bit, drill from the treble side bridge hole to the control cavity. Use a piece of tubing over the bit to protect the edge of the tailpiece hole.
Sand the body to 400 grit.
In control – By now you’re getting the hang of things. Route the control cavity in the body
Careful layout is critical – Make sure the location of the holes is accurate. You don’t want any surprises later.
Drill for the jack – Clamp the body to a stable surface while you drill a ¾' hole to mount the jack.
Ibanez Cavity Depth Bass
Drill some holes – Drill the bridge and tailpiece holes.
Holes for Leads and wires – Drill holes for pick-up leads and ground wire with an extra long twist bit. Protect the wooden body by covering the bit with a piece of tubing.
For Part 2 of this article, click here.
Ibanez Cavity Depth Scale
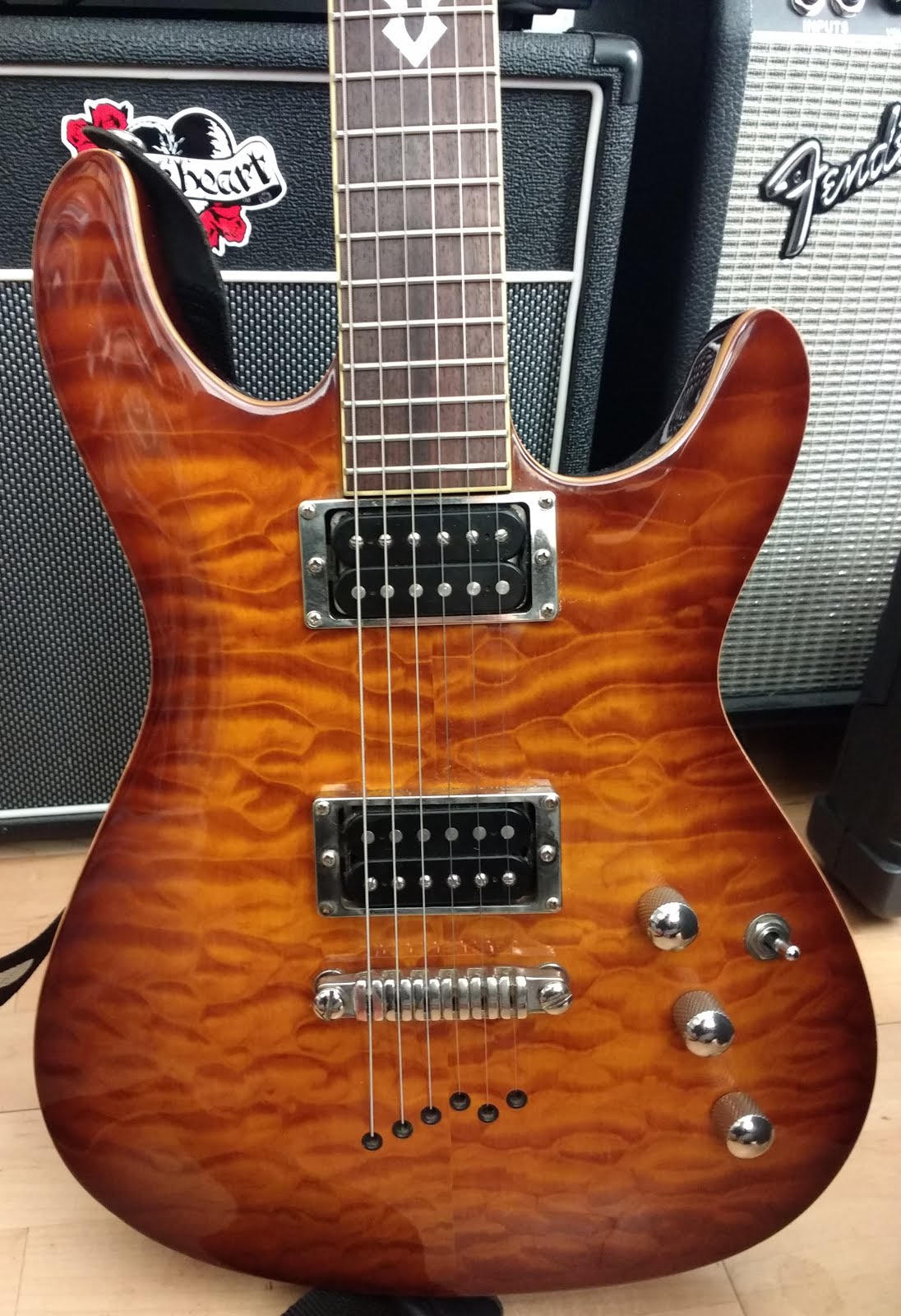